So you want a plane with huge lift capability and the wingspan to match, but you also need it to fit through regular airport gates.
What do you do? If you’re Boeing and the craft is the new 777X, you switch up the game by adding folding wings.
The world got its first glance at this unique innovation on October 3, during a live webcast from Boeing’s factory floor in Everett, Washington, where the first flight-test 777X is being built.
The aircraft is the 777-9X variant, the first of its next-generation 777s, and when it takes to the air it will be the world’s biggest twin-engine jetliner.
It’s a wing thing
Once completed, the 777-9X is to have the widest wingspan of any aircraft in the company’s 102-year history: 235 feet, five inches.
Its hinged wingtips alone measure 12 feet, with locking pins to prevent them from folding during flight.
The wings give the jetliner extra lift, similar to that of a giant sailplane glider, helping the plane to save an overall 12% more fuel than the Airbus A350, according to Boeing.
Now, you might have seen something similar on military aircraft – such as the F/A-18 fighters which need to squeeze onto US aircraft carriers – but when it comes to commercial planes this wing thing is the first of its kind.
In fact, the US Federal Aviation Administration had to draft new regulations just for the 777-9Xand its sister craft, the 777-8X.
While its wingspan is pretty epic, it’s not the biggest out there.
It’s a little smaller than an Airbus A380, the world’s largest passenger airliner, which has a span of 261 feet, five inches.
And it’s a good bit less than the 385-foot span of the upcoming Stratolaunch, which will be used to launchrockets and space planes into orbit. When that flies, it will be the world’s largest airplane.
Static test plane
October’s wing reveal follows on the heels of the “fully assembled” static 777-9X test plane being rolled out at the Everett facility in September.
While it will never take to the skies, the static aircraft is to undergo almost a year of testing on the ground to verify the structural strength and accuracy of the design.
Although the airframe is largely complete, it’s missing some components, such as engines and an avionics system.
Structure and load-bearing

“Static test is our opportunity to verify the design of the structure and load-bearing components of the airplane, ensuring the final product is safe for our customers and the flying public,” says Doreen Bingo, Boeing Test and Evaluation 777X Test Program manager.
“Using a full-scale airplane, we’ll run various load conditions on the wings, gears, the struts and the fuselage.”
The wings have been tested at one-and-a-half-times the designated load during previous static tests, resulting in a wing flexing more than 26 feet.
Engineering revolution
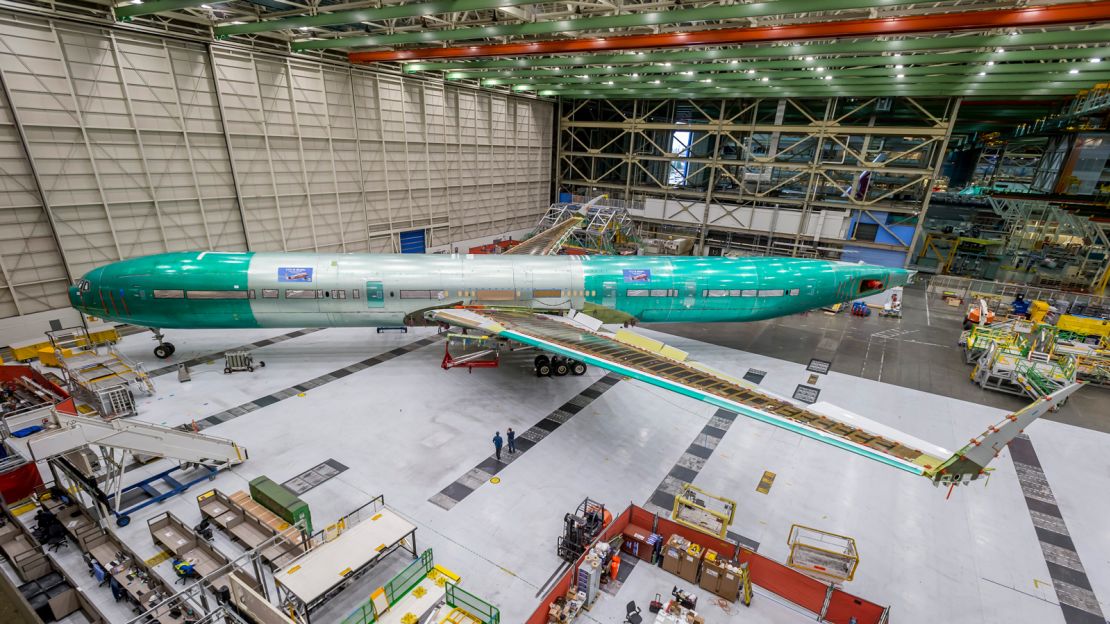
The jet’s fuselage is made of aluminum, like most airliners, but the wings are made of super-strong, light weight carbon fiber, which helps it to save fuel. (That’s why the wings are so flexible.) A special process is required to make the wings, including a huge, custom pressurized oven to bake the carbon fiber material.
Seating 350 to 425 passengers, the airliner is due to debut in 2020, with test flights beginning next year.
Boeing says its operating costs will work out 10% lower than that of the A350-1000.
The plane’s range is expected to reach more than 14,000 kilometers (8,699 miles) – about the distance between Dubai and Panama City.
Several airlines have already placed orders, including Emirates, All Nippon Airways and Lufthansa.
Boeing’s new X family comes as part of an engineering revolution allowing jetliners with only two engines to take on many of the same global routes as larger, fuel-guzzling four-engine airliners such as the 747and Airbus’s A340 and A380 Super Jumbo.
Initial versions of the 777 have been flying for two decades.The X family will come with its own newly designed engine: General Electric’s GE9X, which is currently in testing.
The 777-8X, which will have a longer range but a smaller capacity, is also in the works.
CNN’s Brad Lendon and Thom Patterson contributed to this report.